1. Break across the Chuck Ring Bearing Surface
Probable causes:
– Worn out bit chuck rings
– Insufficient lubrication
– Worn out guide bushing
Suggested actions:
– Check the status of the bit, retaining rings, and guide bushing prior to drilling
– Ensure using appropriate and adequate hammer oil
– Replace aged components of the hammer with new ones
2. Break across the Splines
Probable causes:
– In relation to DTH hammer diameter, the diameter of bit head is too big
– Too much torque
– Worn out driver sub
Suggested actions:
– Modify drill settings for oversized drill bits
– Utilize a larger DTH hammer suitable for the bit size
– Adjust torque according to the rock conditions
– Replace worn out hammer components with new parts
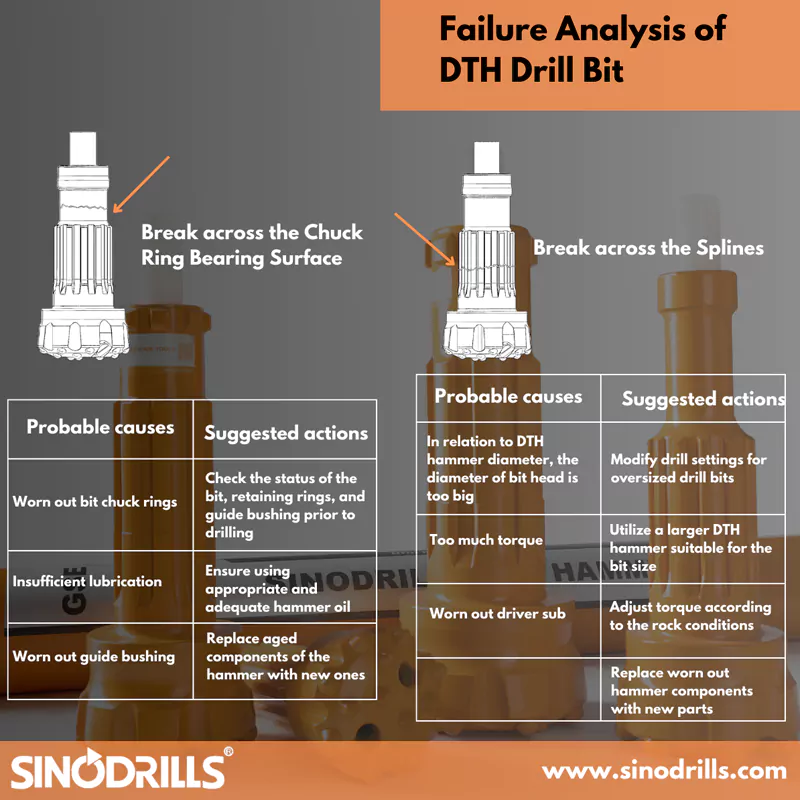
3. Piston Striking Face Breakage
Probable causes:
– Worn out guide bushing
– Worn out piston, bit retaining ring, or driver sub
Suggested actions:
– Check the status of the piston, bit retaining rings, driver sub and
guide bushing prior to drilling
-Replace worn out hammer components with new parts
4. Shoulder damage
Probable causes:
– Incorrect feed force
Suggested actions:
– Adjust feed force to keep the carbide working against the rock; increase on softer rocks but reduce as more drill pipe is added thus naturally increasing the feed force
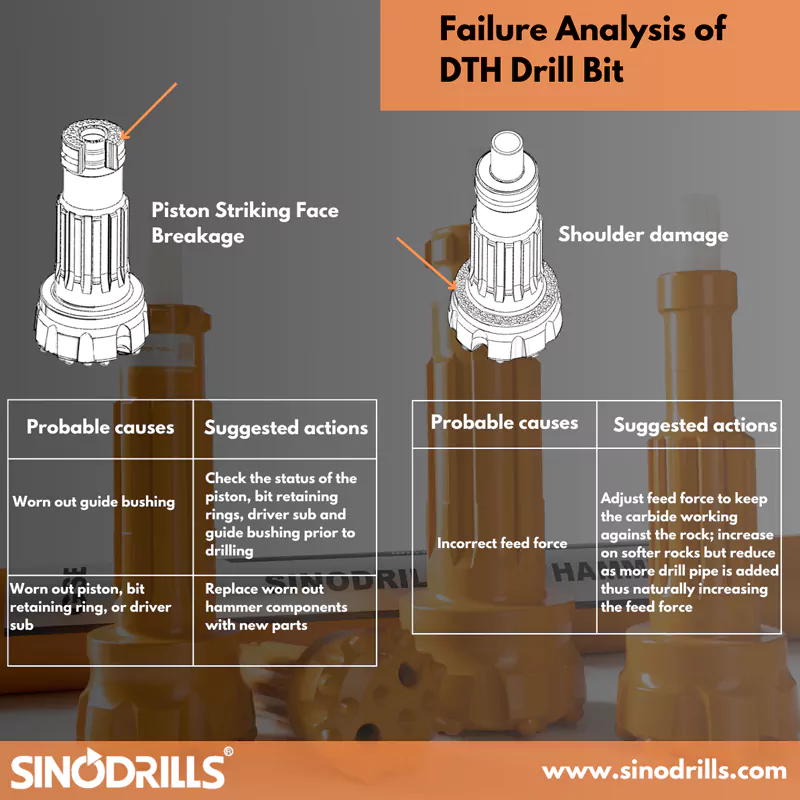
5. Piston striking face damage
Probable causes:
– Inadequate lubrication
– Debris trapped between the bit and piston
Suggested actions:
– Ensure using appropriate and adequate hammer oil
– Maintain tight hammer joints and cleanse the driver sub, bit retaining ring, and drive splines consistently
– Inspect hammer check valve assembly to ensure functionality
6. Broken foot valve
Probable causes:
– Worn out piston, drive splines, or driver sub
– Misalignment
– Lack of lubrication
Suggested actions:
– Check the status of the piston, bit, and driver sub prior to drilling
– Replace worn out hammer components with new parts
– Employ alignment tools and drill practices for straighter boreholes; opt for bits with a concave face design
– Use suitable and sufficient hammer oil
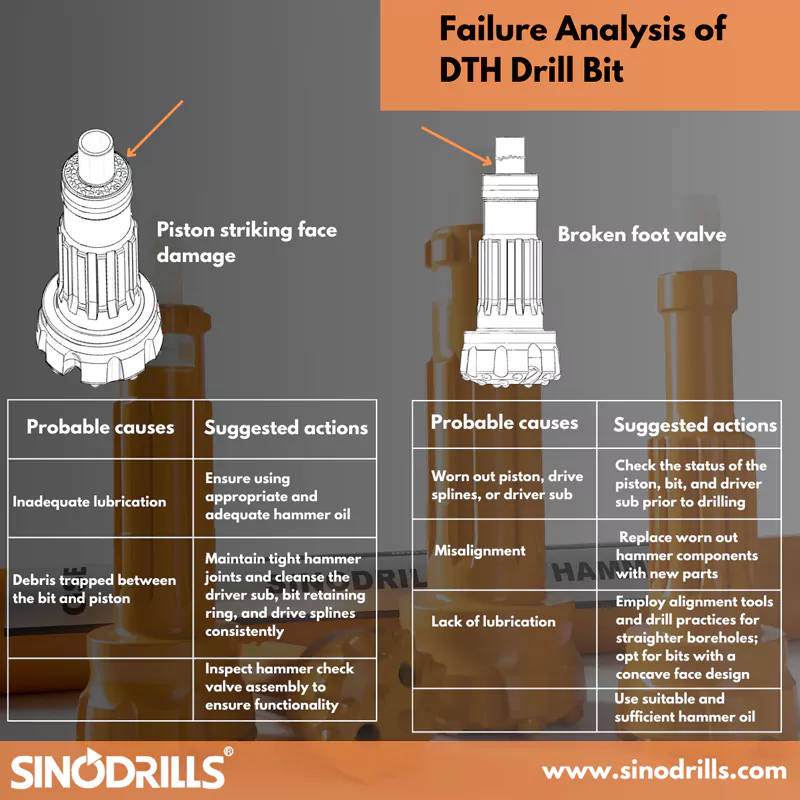