1. Dented, chipped, or damaged striking end
Probable causes:
– Beginning percussion or rotation with the shank end placed against the coupling’s shoulder
– Feed misaligned
– Misalignment from hole deviation
Suggested actions:
– Avoid initiating percussion or rotation unless the shank thread is perfectly aligned inside the coupling
-Ensure the feed mechanism operates aligns properly
-Take action to drill straighter holes; use bits with drop center face design and/or retract body
-Do not thread the rod beyond the middle of the coupling
2. Longitudinal crack
Probable causes:
-Drilling with loose thread joints
-Reversing rotation while percussion is active
-Dents on the steel surface
-Hole deviation
-Worn-out sleeve
Suggested actions:
-Ensure all joint connections are securely tightened before beginning percussion
-Avoid reversing rotation during percussion
-Take action to drill straighter holes; use bits with drop center face design and/or retract body
-Replace worn-out sleeve
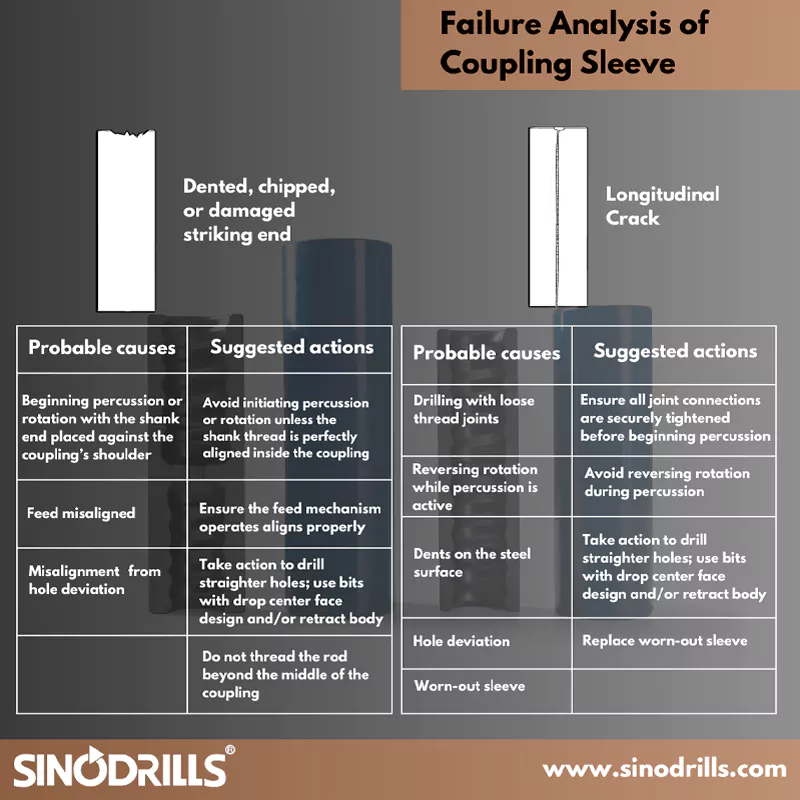
3. Transversal crack
Probable causes:
-Dents on surface of steel
-Worn-out sleeve
-Misalignment from hole deviation
-Insufficient feed pressure
-Excessive rotational force from the use of worn bits
-Thread mismatches
Suggested actions:
-Refrain from hammering or striking the outside of the coupling
-Replace worn out couplings or drill rods
-Adjust drilling practices to achieve a straighter hole
-Modify feed pressure according to the specific rock conditions
-Regrind the bit when wear flats reach up to 1/3 of the button diameter
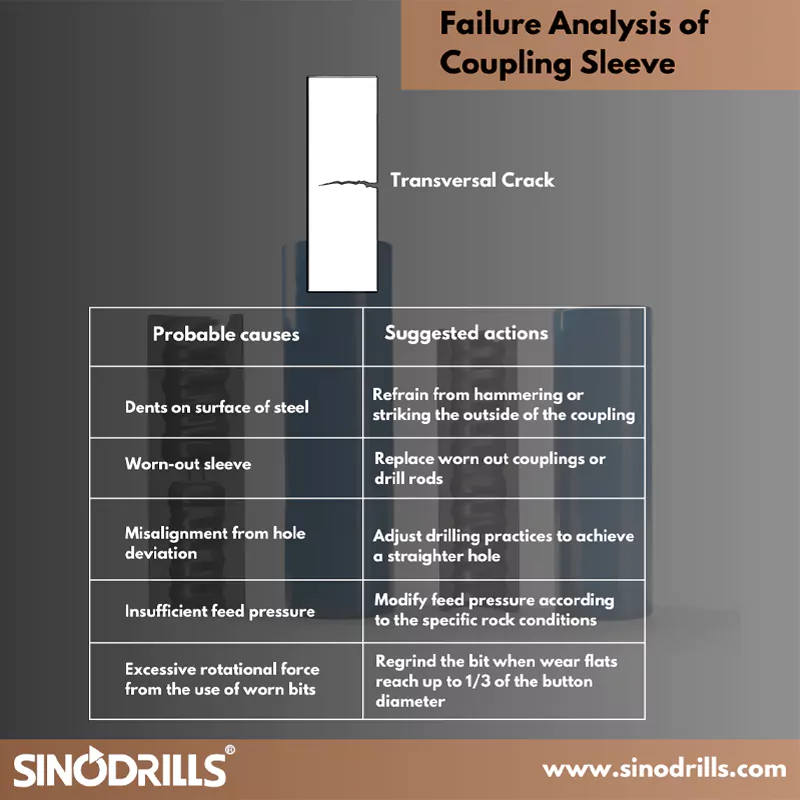