1. Failure Across Female Threads
Probable causes:
-Hole deviation or drill string misalignment
-Insufficient feed pressure
-Excessive torque due to use of worn drill bits
-Mismatched threads
-Dents or deformations on the steel surface
Suggested actions:
-Use guide tools and bits designed with a drop center face or retract body
-Adjust feed pressure based on the rock conditions
-Sharpen dull carbide tips on the bit in accordance with recognized sharpening processes
-Avoid mixing drill string components from different manufacturers
-Use proper wrenches for loosening joints
-Avoid hitting outside the area of the joint
2. Deformation of female end
Probable causes:
-Drilling with loose thread connections
-Misalignment during the threading of drill rods, resulting in impacts against the coupling shoulder
Suggested actions:
-Ensure thread connections are securely tightened prior to beginning percussion drilling
-Align drill rods correctly before threading them together
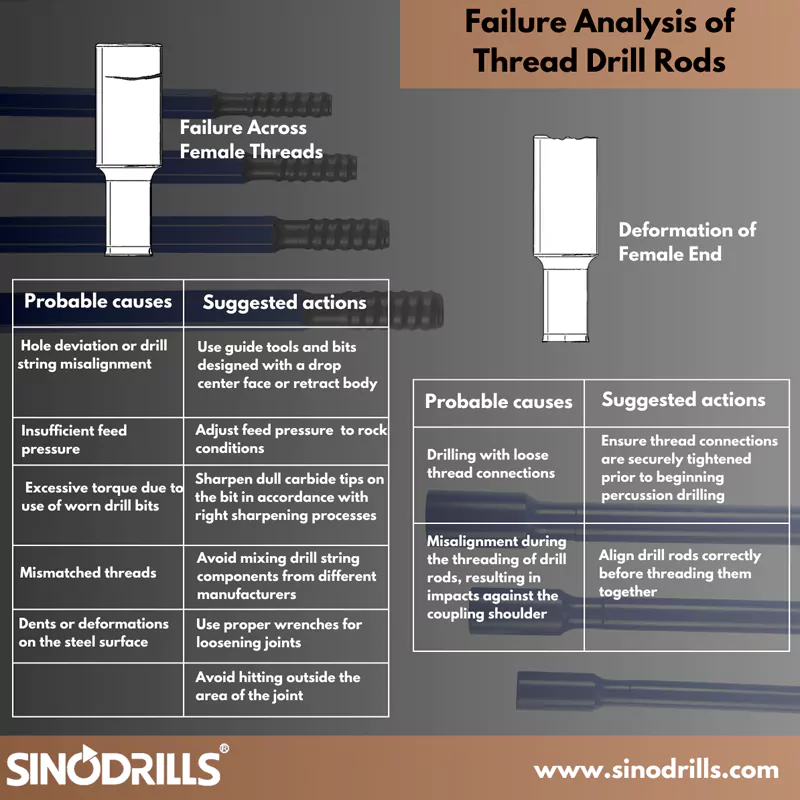
3. Vertical crack on the female end
Probable causes:
-Hole deviation
-Worn-out thread condition
-Misalignment when assembling drill rods
-Drilling with loose thread joints
Suggested actions:
-Focus on drilling more straighter holes
-Replace worn out components of the drill string in time
-Ensure tightness of joints before starting to drill
-Align drill rods correctly prior to threading
4. Pitting or Wear in Threads
Probable causes:
-Overheating of threads due to loose connection or hole deviation
-Reflected percussive energy
-Dry firing or free hammering
-Drilling of worn-out bits
Suggested actions:
-Initiate percussion only when the bit is correctly engaged with the rock
-Sharpen dull carbides on the bit following appropriate procedures
-Replace worn-out drill string parts; avoid coupling worn bits or rods with new ones
-Fine-tune percussion and feed pressure based on drilling conditions
-Employ proper type and adequate lubrication, check often
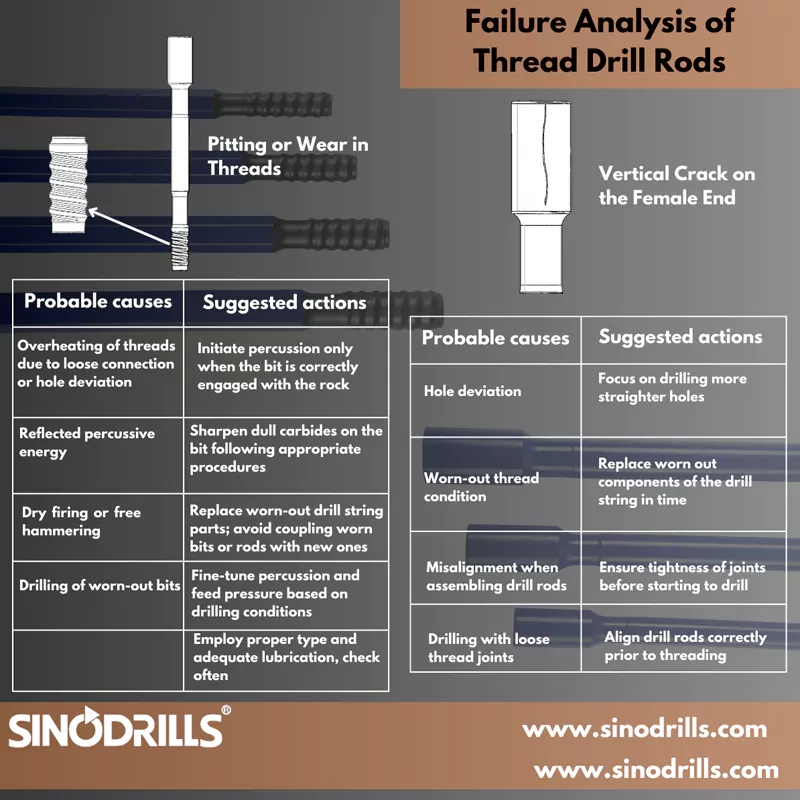
5. Failure at The Beginning of the Thread
Probable causes:
-Worn threads
-Bending from feed overpressure, or misalignment
-High rotational forces from using a worn bit resulting in high energy feedback
-Poor drilling conditions or unstable rock formations
-Persisting percussion with a stuck rod
-Bending due to poor alignment
Suggested actions:
-Replace worn drilling components; ensure changes of couplings and rods are done simultaneously
-Adjust feed pressure to prevent drill string bending
-Follow proper sharpening methods for dull carbides
-Optimize drilling parameters suitable to the rock conditions
-Use bits featuring a drop center face or retract body
-Avoid engaging percussion with a stuck drill string
6. Male end broken at face
Probable causes:
-Insufficient feed pressure
-Use of dull drill bits
-Worn threads on couplings or bits
-Misalignment when connecting drill rods
-Corrosion-induced fatigue failure
Suggested actions:
-Replace worn-out components; never mount a worn coupling on a new rod
-Timely maintenance of button bits
-Set feed pressure according to the rock conditions
-Ensure proper alignment during rod threading
-Use extensions to better align drilling components
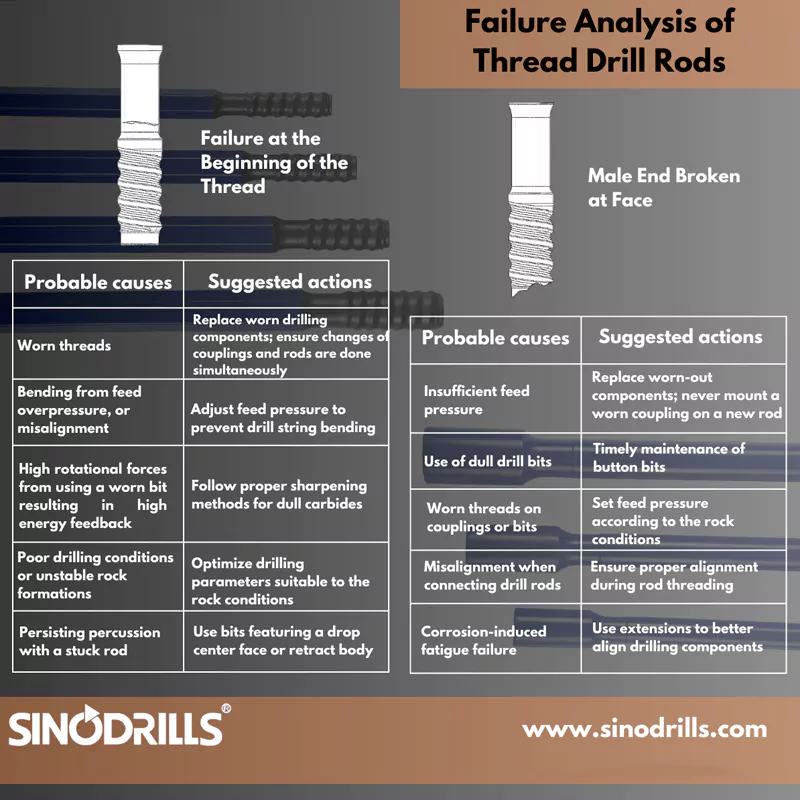
7. Inner surface compromised
Probable causes:
-Corrosive damage from flushing agents
-Insufficient rust protection
-Presence of pores on flushing hole surfaces
Suggested actions:
-Maintain or replace flushing agents as necessary
-Implement appropriate storage methods
-Change out components with higher frequency
8. Outer surface compromised
Probable causes:
-Bending from misalignment
-Excessive feeding pressure
-External damage from the rod rubbing against steel surfaces
-Improper handling and care
-Challenging drilling conditions
-Hammer strikes
Suggested actions:
-Ensure regular maintenance of the drilling rig
-Verify the good condition of centralizers
-Use alignment tools and enhance drilling practices for straighter drilling; consider bits with drop center face designs or retractable bodies
-Adjust feed pressure according to rock conditions
-Avoid striking the drill rod from outside; employ suitable wrenches for loosening joints
-Store rods on racks rather than on the ground;
-Adjust drilling parameters to rock conditions
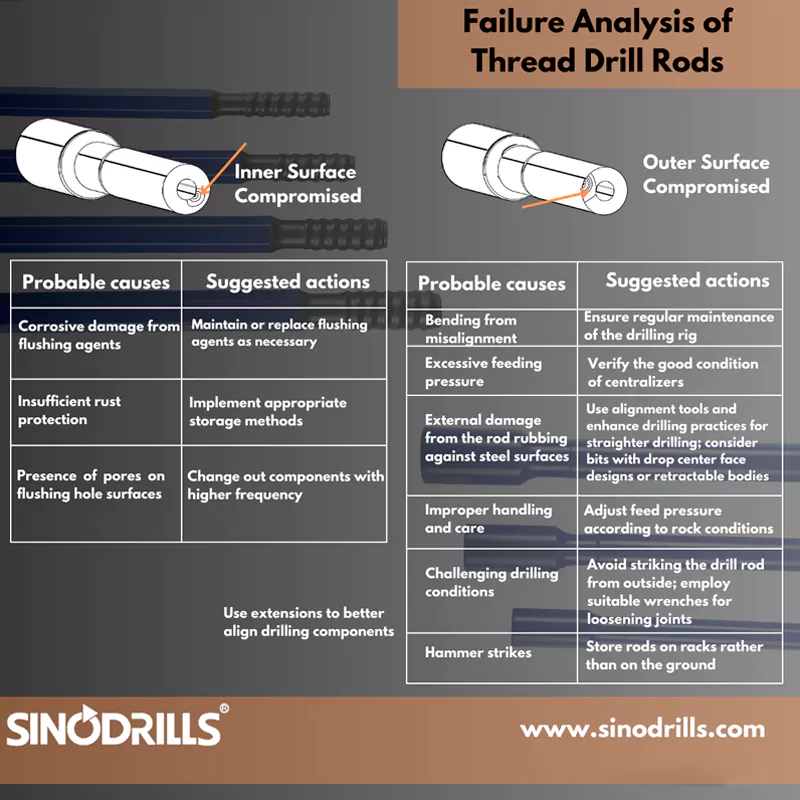